製品設計におけるヒケ発生箇所の予測と対策
本稿の目標:ヒケ発生前に対策できるようになる!
以前の記事の中で、ヒケの発生メカニズムと対策の改善メカニズム、対策選定の際のポイントについて述べました。またその中で、ヒケ対策は上流工程ほど対策が容易であると述べました。つまり、製品設計→金型設計→成形という流れの中で、左側ほど対策が容易になるということです。
であれば、もっとも大事なのは設計時にヒケを的確に予想することになります。そうであれば、これは書かねばならない!ということで、設計時にヒケの発生を予想する方法について解説します。
A. 肉厚から確認する
ヒケを予想する際に着目すべきポイントとしては、成形品の肉厚、ゲートからの距離や流露の太さ、金型における熱溜まり、などがあります。ここでは、まず肉厚からヒケ発生を予想する方法についてのべます。
①絶対肉厚
よく言われるとおり、成形品の肉厚が厚いほどヒケが発生しやすくなります。ヒケが発生しないための上限は1mmとも3mmとも言われますが、これは樹脂の種類や成形条件によって大きく変化するため、あまり意味はありません。1mmでヒケが生じることもあれば、30mmでも生じないこともあります。
正直なところ、同じ樹脂、形状、成形条件であれば、肉厚が大きくなるほどヒケが生じる可能性は高くなる、という程度しか言えません。むしろ次の相対的な肉厚(差)にこそ注目する必要があります。
②相対肉厚
成形品の肉厚が変化する箇所では、ヒケが生じやすくなります。肉厚が薄い箇所に比べて厚い箇所では、固化の際の収縮量も大きくなり、周辺を引っ張る収縮力も大きくなります。
そのため、薄い箇所と厚い箇所が隣接した場合、その境界付近では収縮力がアンバランスとなり、多くの場合薄い箇所のスキン層が厚い箇所の内部固化に引きずられる形でヒケが発生します。
かといって肉厚差がまったくない成形品も稀だと思いますので、大事なのはその肉厚差がヒケにつながるものなのか、対策をどうすればよいのか、ということになります。
では、具体的にどういうステップで対応していくのかを以下で解説していきます。
ヒケ発生可能性の判断方法
まずヒケにつながるかどうかの判断ですが、成形品断面に内接円を描き、その大きさの変化の様子を見る方法が有効です。
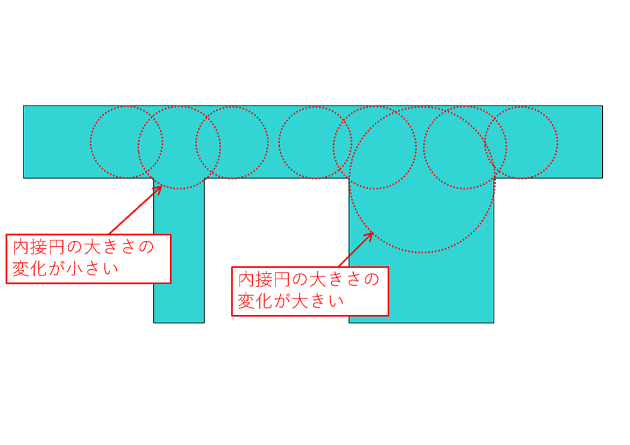
図1は一例ですが、リブが2ヶ所見られます。リブの長さは同じですが、左側のリブの肉厚は成形品表面の半分程度であるのに対し、右側は倍程度です。この成形品断面に内接円を描きます。左側のリブによる内接円の大きさの変化はわずかですが、右側のリブによる内接円の大きさの変化は大きく、かつ急激です。
ヒケが生じやすいのはもちろん右側のような場合です。右側のリブには大きな体積差が存在するため、それが固化する際に巨大な収縮力の差を生じ、周辺のスキン層を変形させてヒケを生じさせます。
ヒケ対策方法
対策としては、できる限り肉厚差を減らす、もしくは肉厚変化を緩やかにすることです。
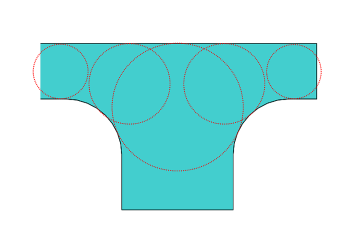
例えば図2のように成形品に隅Rを設けてやることでRに沿って内接円が変化するため、肉厚変化の度合いが幾分か緩やかになります。また以前の記事で述べたように、成形時の金型温度を下げてスキン層を厚くするというような方法もありますが、本稿ではあくまで設計面に着目することとし、割愛します。
内接円を用いた方法の注意点
さて、この内接円を用いた方法ですが、一つだけ注意点があります。
それは、精度よく予想するためには、1方向からの肉厚差の確認に加えて、少なくとも残り2方向から大きな肉厚の存在を確認する必要があるということです。先ほど述べたとおり、肉厚差による体積差がヒケを生じさせます。そして体積とは3次元量です。そのため3方向から見ないと体積変化がどうなっているかは厳密にはわからないからです。
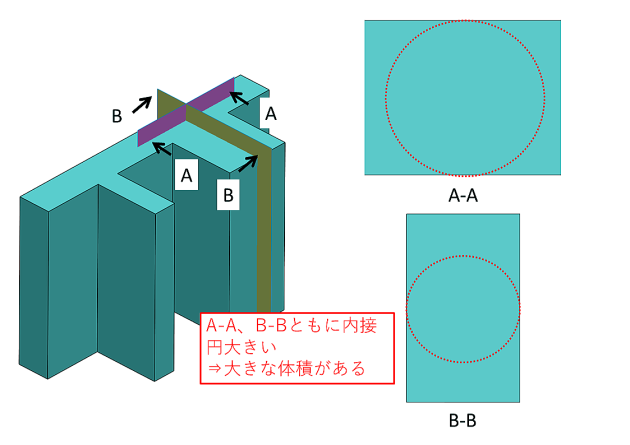
例えば先ほどの図1の例ですが、確かにこの断面では肉厚差があるものの、これだけでは体積差がある可能性があるとしか言えません。もしこの成形品が図3のように高さ方向にも十分に厚みがあれば、他の2断面についても大きな内接円が描けるため、ここに巨大な体積があることがわかります。
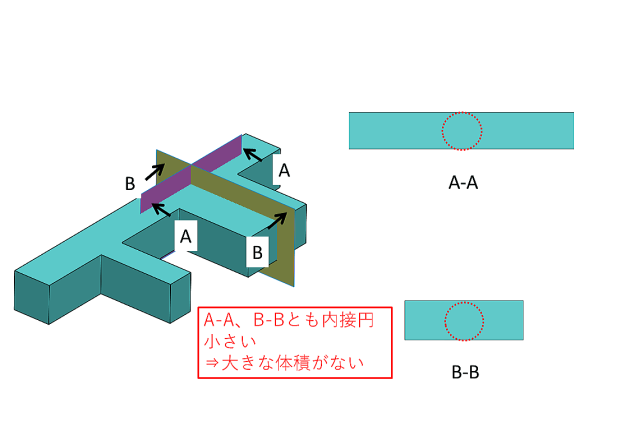
逆に図4のように高さが小さい成形品であった場合には、他の2断面では大きな内接円は見られず、大きな体積は存在しないことがわかります。このように、肉厚差は1つの断面で確認できれば十分ですが、同時に残り2つの断面でも大きな肉厚が確認できたとき、体積差によるヒケが生じる可能性が高まります。
B.ゲート位置や樹脂流路の太さから確認する
ヒケは、既に固化したスキン層などが、遅れて固化する内部樹脂の収縮に引っ張られることで生じます。そのため、もし内部樹脂の収縮を補うような補充がなされた場合、ヒケは生じにくくなります。
このときに大事になのが、ゲートからの距離や途中の樹脂流路の太さです。距離が近く、かつ流路が太い方が途中での圧力低下も少なくなるため、補充もされやすくなります。逆から言えば、ゲートから遠く、かつ入り組んだ流路の先に大きな体積差が存在する場合、そこでヒケが生じる可能性はさらに高くなります。
この点については、ゲートの配置や大きさ、ゲート付近の肉厚といった金型設計や、成形時の保圧条件などによっても影響を受けますが、ここでは詳細は割愛します。
C.金型の熱溜りから確認する
熱溜りとは、周辺に比べて放熱が遅いといった理由で、周辺より高温になやすい箇所を指します。
熱溜りの例
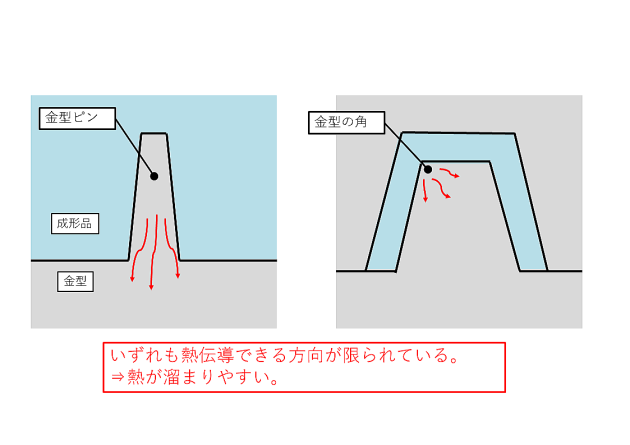
代表的な例としては図5左のような金型のピン部分です。通常、金型の冷却は金属の熱伝導による放熱によって進みます。しかしこのような行き止まりのピン部分については、熱伝導の方向が極めて限定されていて断面積が小さいため、放熱が遅くなります。結果としてピン先端は周辺よりも高温になり、この近くの樹脂の固化はおくれます。
そのため、遅れて固化する際に周辺のスキン層をヒケさせたり、ピンによって成形された穴の内面がヒケたりします。成形開始時には何ともなかったが、成形をつづけるうちに熱溜り部が高温になりヒケが生じ始めることもあります。
またピン部分ほど極端ではないにしても、図5右のような金型の角部についても熱溜り発生の可能性があります。
熱溜りへの対応方法
これを防ぐためには、ピンの冷却を強化することは当然ながら有効です。できるだけ太く短くしたり、製品を貫通穴として、金型ピンの放熱方向を増やしたりといった方法が考えられますが、製品設計上できない場合も多いと思います。
そのため、肉厚を薄くしたりといった製品設計による対応と合わせて、熱溜りの近くに冷却配管を設けたり、より熱伝導のよいベリリウム銅のような材料を金型に用いたりするなど、金型設計での対応も重要となってきます。
まとめ
製品設計段階においてヒケの発生を予想するための方法と対策を、肉厚、ゲートとの位置関係、金型の熱溜りという、大きく3つの視点からお伝えしてきました。これらは互いに独立した視点であり、当てはまる数が多いほど、その部分でヒケが生じる可能性は高くなってきます。
まず肉厚に注目して急激な体積差が見られる箇所を洗出し、それらの箇所をゲートからの距離や熱溜りの視点からも検討して、より危険度の高い箇所から優先的に対策を検討していくとよいでしょう。製品単体での対策が難しい場合は、金型屋さんや成形屋さんも巻き込んで対策を検討するのもとても有効な方法であり、おすすめです。
ディスカッション
コメント一覧
まだ、コメントがありません